New steel silo design helps cement storage to upgrade to smart technology
Cement Storage Status and Challenges
With the continuous development of international infrastructure construction and the acceleration of urbanization, the demand for cement as a basic building material has remained high. However, traditional cement storage methods are facing many challenges, which seriously restricts the modernization of the cement industry.
At present, cement storage mainly adopts the following methods: bag storage and warehouse storage. A few enterprises adopt bulk storage in closed factories. Bulk storage is the most primitive method. Cement is exposed to the air and is greatly affected by the weather. It is easy to clump. A lot of dust will be generated during production operations. Bulk storage not only affects the quality of cement, but also harms human health and the environment. Bag storage fills cement in small bags or large bags, which can extend the shelf life of cement. However, bag storage has high packaging costs and occupies space. In addition, the transportation of bagged cement requires a lot of manpower and equipment, and the production cost is high. It is usually used for small batches of cement retail. For silo storage, the industry used to use reinforced concrete silos for storage. Reinforced concrete silos have the advantages of reliable structure and long service life, but they have long construction period, high construction cost and poor plasticity. In the face of the increasingly fierce market competition, reducing investment costs and achieving benefits in a shorter time have become issues that companies pay more attention to.
These traditional storage methods generally have several prominent problems: high storage loss rate (generally 3%-5%), serious environmental pollution, large floor space, low efficiency of warehousing, and difficulty in achieving accurate measurement and information management. Especially in the context of increasingly stringent environmental protection requirements and rising labor costs, the disadvantages of traditional storage methods are becoming more and more prominent.
In addition, with the advancement of cement production technology and the increase in product types, higher requirements are also placed on storage conditions. Different types and grades of cement require different storage environments and turnover cycles, and traditional storage methods are difficult to meet the needs of such refined management. The industry is in urgent need of a new type of efficient, environmentally friendly and intelligent storage solution, and the innovative development of steel silo technology provides a possibility for this demand.
.jpg)
Significant advantages of steel silo for cement storage
Compared with traditional storage methods, steel silos have shown all-round competitive advantages and have become the preferred solution for modern cement storage. The core advantages of steel silos for cement storage are reflected in three aspects: structural performance, economic benefits and environmental performance.
From the perspective of structural performance, steel silos are generally divided into three types: welded silos, bolted silos and spiral silos. Welded silos are welded with steel plates, bolted silos are prefabricated steel plate modules , assembled on site by bolts, and spiral silos are made of galvanized steel coils, which are continuously bitten by the on-site spiral plate rolling machine (without welding) to form a circular silo wall, and the bite seam is spirally rising. The overall structure is stable and reliable. The steel silo is simple to construct and has a short construction period. The silo wall can be painted, hot-dip galvanized or made of stainless steel according to needs. The steel silo has a design life of 25 years. The airtightness of the steel silo is far superior to that of traditional concrete silos, which can effectively isolate external moisture and rainwater, keep the humidity in the silo below 60%, and prevent cement agglomeration. The unique fluidization system design ensures smooth discharge, with a discharge rate of up to 95%.
In terms of economic benefits, the cost of steel silos is only 60%-70% of that of concrete silos, and the construction period is shortened by more than 50%, so they can be put into use quickly. Steel silos adopt modular design, which is convenient for expansion and can flexibly adjust the capacity according to demand. Due to its light weight, the cost of basic treatment is greatly reduced. What is more worth mentioning is that the maintenance of steel silos mainly involves rust removal and repainting, and the maintenance cost is low. The high degree of automation also significantly reduces labor costs. A 10,000-ton steel silo only needs 1-2 people to manage it.
Environmental protection is another highlight of the steel silo. The fully enclosed structure completely prevents dust from spilling out, and with the dust removal system, the dust emission concentration is less than 20mg/m³, which is far better than the international standard. Compared with traditional storage methods, steel silos can reduce cement loss, ensure cement quality, and have significant economic and environmental benefits.
It is particularly noteworthy that steel silos provide an ideal basic platform for intelligent management. It is easy to install various sensors and automation equipment, and smoothly connect to the Internet of Things system. This feature makes steel silos the best carrier for the intelligent upgrade of cement storage, laying a physical foundation for the digital transformation of the industry.
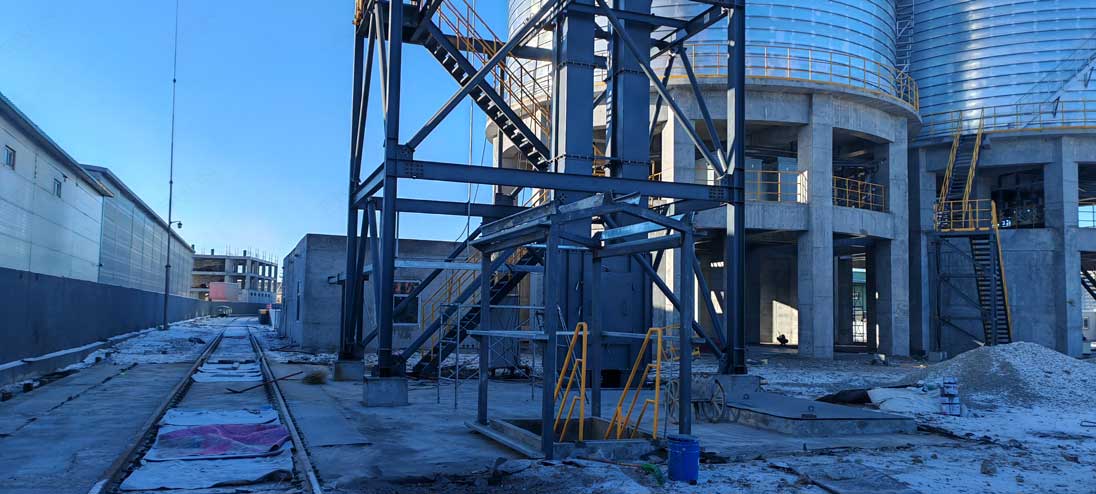
Technical innovations in the design of new steel silo
Modern steel silo design has broken through the limitations of traditional storage silos and achieved a qualitative leap in performance through a series of technological innovations. These innovative designs not only improve the functionality of the steel silo itself, but also provide hardware support for intelligent cement storage.
In terms of structural design innovation, the new generation of steel silos adopts computer-aided design and finite element analysis to achieve structural optimization. For large steel silos, fluidizing air is used to keep cement fluidized to ensure smooth discharge without compaction. The unique multi-point unloading design allows for different discharge locations to be selected as needed. The steel silo can be designed according to specific needs in terms of silo diameter, height, cone bucket, inlet and outlet, etc., to adapt to various working conditions such as new construction and renovation projects.
Another highlight is the breakthrough in material technology. The use of high-strength wear-resistant steel plates extends the service life of key parts by more than 30%. The application of nano-level anti-corrosion coating enables the steel silo to withstand various corrosive environments. The addition of new thermal insulation materials effectively reduces temperature fluctuations in the silo and maintains stable cement quality.
Intelligent integrated design constitutes the core competitiveness of the third-generation steel silo. The silo is pre-installed with a variety of sensor installation interfaces, which can monitor key parameters such as material level, temperature, and pressure in real time. The built-in RFID identification system can track and manage different batches of cement. The automatic metering system has an accuracy of ±0.5%, far exceeding the level of manual metering. The remote monitoring interface supports seamless connection with the central control system, providing a hardware foundation for intelligent storage management.
The innovation in energy-saving design is particularly worth mentioning. The new steel silo adopts a solar-assisted heating system to reduce energy consumption for moisture prevention in winter. The intelligent ventilation system automatically adjusts the air exchange rate according to environmental conditions, minimizing energy consumption while ensuring cement quality.
These technological innovations are not isolated, but mutually supportive and system-integrated. It is this all-round design advancement that makes the new steel silo no longer a simple storage container, but an intelligent cement management platform, providing unlimited possibilities for subsequent digital upgrades.
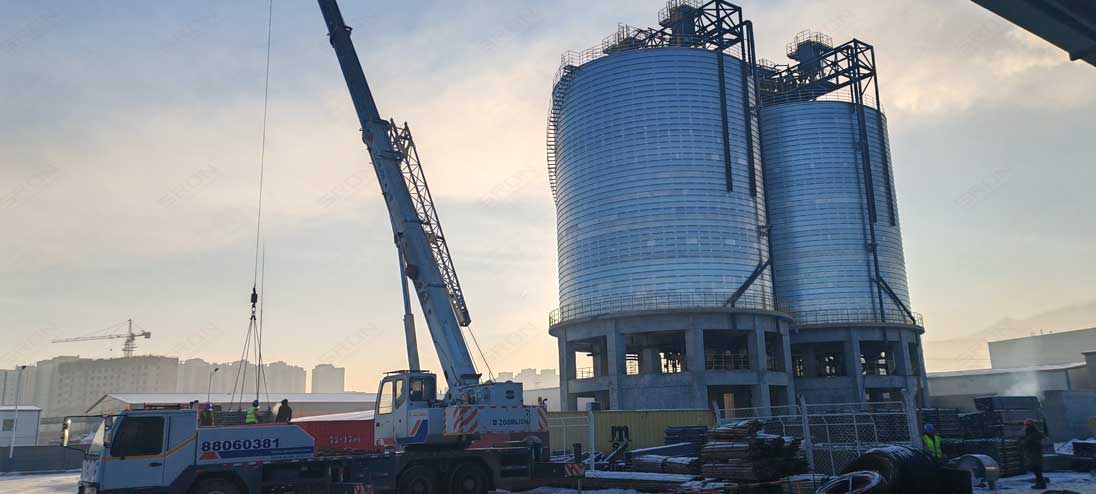
Looking ahead, intelligent steel silos will be more closely integrated with cement production processes and become an important part of the intelligent manufacturing system. It may develop into a multifunctional platform integrating storage, homogenization, and distribution, and even integrate simple secondary processing functions. With the popularization of technology, intelligent steel silos will be popularized from large enterprises to small and medium-sized enterprises, promoting the balanced development of the entire industry.
With the continuous development of international infrastructure construction and the acceleration of urbanization, the demand for cement as a basic building material has remained high. However, traditional cement storage methods are facing many challenges, which seriously restricts the modernization of the cement industry.
At present, cement storage mainly adopts the following methods: bag storage and warehouse storage. A few enterprises adopt bulk storage in closed factories. Bulk storage is the most primitive method. Cement is exposed to the air and is greatly affected by the weather. It is easy to clump. A lot of dust will be generated during production operations. Bulk storage not only affects the quality of cement, but also harms human health and the environment. Bag storage fills cement in small bags or large bags, which can extend the shelf life of cement. However, bag storage has high packaging costs and occupies space. In addition, the transportation of bagged cement requires a lot of manpower and equipment, and the production cost is high. It is usually used for small batches of cement retail. For silo storage, the industry used to use reinforced concrete silos for storage. Reinforced concrete silos have the advantages of reliable structure and long service life, but they have long construction period, high construction cost and poor plasticity. In the face of the increasingly fierce market competition, reducing investment costs and achieving benefits in a shorter time have become issues that companies pay more attention to.
These traditional storage methods generally have several prominent problems: high storage loss rate (generally 3%-5%), serious environmental pollution, large floor space, low efficiency of warehousing, and difficulty in achieving accurate measurement and information management. Especially in the context of increasingly stringent environmental protection requirements and rising labor costs, the disadvantages of traditional storage methods are becoming more and more prominent.
In addition, with the advancement of cement production technology and the increase in product types, higher requirements are also placed on storage conditions. Different types and grades of cement require different storage environments and turnover cycles, and traditional storage methods are difficult to meet the needs of such refined management. The industry is in urgent need of a new type of efficient, environmentally friendly and intelligent storage solution, and the innovative development of steel silo technology provides a possibility for this demand.
.jpg)
Significant advantages of steel silo for cement storage
Compared with traditional storage methods, steel silos have shown all-round competitive advantages and have become the preferred solution for modern cement storage. The core advantages of steel silos for cement storage are reflected in three aspects: structural performance, economic benefits and environmental performance.
From the perspective of structural performance, steel silos are generally divided into three types: welded silos, bolted silos and spiral silos. Welded silos are welded with steel plates, bolted silos are prefabricated steel plate modules , assembled on site by bolts, and spiral silos are made of galvanized steel coils, which are continuously bitten by the on-site spiral plate rolling machine (without welding) to form a circular silo wall, and the bite seam is spirally rising. The overall structure is stable and reliable. The steel silo is simple to construct and has a short construction period. The silo wall can be painted, hot-dip galvanized or made of stainless steel according to needs. The steel silo has a design life of 25 years. The airtightness of the steel silo is far superior to that of traditional concrete silos, which can effectively isolate external moisture and rainwater, keep the humidity in the silo below 60%, and prevent cement agglomeration. The unique fluidization system design ensures smooth discharge, with a discharge rate of up to 95%.
In terms of economic benefits, the cost of steel silos is only 60%-70% of that of concrete silos, and the construction period is shortened by more than 50%, so they can be put into use quickly. Steel silos adopt modular design, which is convenient for expansion and can flexibly adjust the capacity according to demand. Due to its light weight, the cost of basic treatment is greatly reduced. What is more worth mentioning is that the maintenance of steel silos mainly involves rust removal and repainting, and the maintenance cost is low. The high degree of automation also significantly reduces labor costs. A 10,000-ton steel silo only needs 1-2 people to manage it.
Environmental protection is another highlight of the steel silo. The fully enclosed structure completely prevents dust from spilling out, and with the dust removal system, the dust emission concentration is less than 20mg/m³, which is far better than the international standard. Compared with traditional storage methods, steel silos can reduce cement loss, ensure cement quality, and have significant economic and environmental benefits.
It is particularly noteworthy that steel silos provide an ideal basic platform for intelligent management. It is easy to install various sensors and automation equipment, and smoothly connect to the Internet of Things system. This feature makes steel silos the best carrier for the intelligent upgrade of cement storage, laying a physical foundation for the digital transformation of the industry.
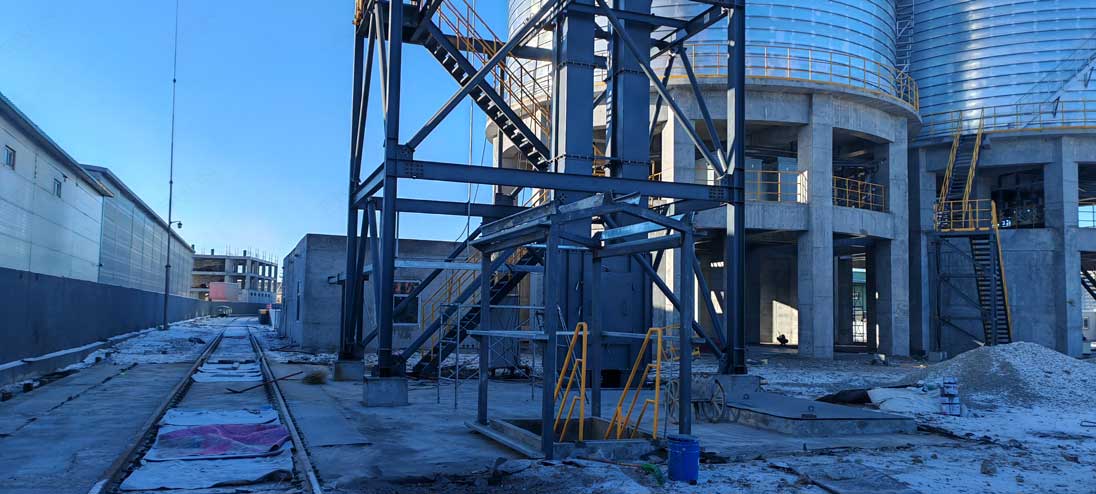
Technical innovations in the design of new steel silo
Modern steel silo design has broken through the limitations of traditional storage silos and achieved a qualitative leap in performance through a series of technological innovations. These innovative designs not only improve the functionality of the steel silo itself, but also provide hardware support for intelligent cement storage.
In terms of structural design innovation, the new generation of steel silos adopts computer-aided design and finite element analysis to achieve structural optimization. For large steel silos, fluidizing air is used to keep cement fluidized to ensure smooth discharge without compaction. The unique multi-point unloading design allows for different discharge locations to be selected as needed. The steel silo can be designed according to specific needs in terms of silo diameter, height, cone bucket, inlet and outlet, etc., to adapt to various working conditions such as new construction and renovation projects.
Another highlight is the breakthrough in material technology. The use of high-strength wear-resistant steel plates extends the service life of key parts by more than 30%. The application of nano-level anti-corrosion coating enables the steel silo to withstand various corrosive environments. The addition of new thermal insulation materials effectively reduces temperature fluctuations in the silo and maintains stable cement quality.
Intelligent integrated design constitutes the core competitiveness of the third-generation steel silo. The silo is pre-installed with a variety of sensor installation interfaces, which can monitor key parameters such as material level, temperature, and pressure in real time. The built-in RFID identification system can track and manage different batches of cement. The automatic metering system has an accuracy of ±0.5%, far exceeding the level of manual metering. The remote monitoring interface supports seamless connection with the central control system, providing a hardware foundation for intelligent storage management.
The innovation in energy-saving design is particularly worth mentioning. The new steel silo adopts a solar-assisted heating system to reduce energy consumption for moisture prevention in winter. The intelligent ventilation system automatically adjusts the air exchange rate according to environmental conditions, minimizing energy consumption while ensuring cement quality.
These technological innovations are not isolated, but mutually supportive and system-integrated. It is this all-round design advancement that makes the new steel silo no longer a simple storage container, but an intelligent cement management platform, providing unlimited possibilities for subsequent digital upgrades.
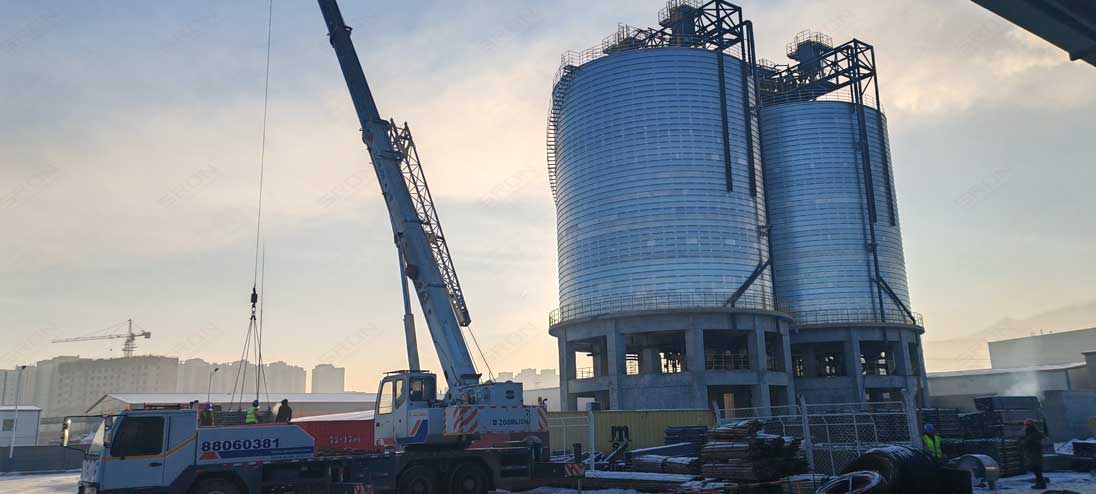
Looking ahead, intelligent steel silos will be more closely integrated with cement production processes and become an important part of the intelligent manufacturing system. It may develop into a multifunctional platform integrating storage, homogenization, and distribution, and even integrate simple secondary processing functions. With the popularization of technology, intelligent steel silos will be popularized from large enterprises to small and medium-sized enterprises, promoting the balanced development of the entire industry.